Prototype Gear Manufacturing Service
Narutaki industries utilizes a wide range of materials and processing techniques to handle high-precision custom gear prototypes, from design support to small-scale production. By improving the perfection of the product from the prototype stage, we can achieve optimal gear design and contribute to accelerating product development.
Supported Gear Specifications
Item | Specifications | |
---|---|---|
Number of Modules (max.) | 4 | |
Diametral Pitch (min.) | 6.5 | |
Outer Diameter (max.) | φ100 | |
Machining Material | Carbon Steel | S45C(AISI 1045) |
Alloy Steel | SCM415(AISI 4115), SCM420(AISI 4118), SCM435(AISI 4135), SCM440(AISI 4140), SNCM420(AISI 4320) | |
Stainless Steel | SUS304(AISI 304) | |
Machining Equipment | 5-axis multi-tasking machine DMG Mori, NTX1000 | |
Spiral Bevel Gear SBG-10×11 | ||
CNC Cylindrical Grinder, E300G | ||
NC grinding machine for spiral bevel gears (module: ~4, DP: 6.5~) |
Types of Gears We Manufacture
Spiral bevel gears
Spiral bevel gears are a type of bevel gear with curved, angled teeth that allow for smoother and quieter operation compared to straight bevel gears. The curved teeth enable gradual engagement, making these gears well-suited for applications requiring high-speed or high-torque transmission, such as in automotive differentials, industrial machinery, and power tools. The design allows for efficient power transmission at 90-degree angles between intersecting shafts.
Straight bevel gears
Straight bevel gears are a type of bevel gear with straight teeth that converge toward the apex of the gear's cone shape. These gears are used to transmit power between intersecting shafts, typically at a 90-degree angle. Unlike spiral bevel gears, straight bevel gears engage abruptly, leading to more noise and vibration, making them better suited for low-speed applications. They are commonly used in mechanical devices where simplicity and durability are key, like hand drills, differential gears, and some industrial machinery.
Zerol bevel gears
Zerol bevel gears are a specialized type of bevel gear characterized by curved teeth with a zero-degree spiral angle at the midpoint of the face width. This design combines features of both straight and spiral bevel gears, offering smooth operation, reduced thrust force, bidirectional rotation.
Zerol bevel gears suitable for applications requiring precision and minimal vibration, such as in automotive steering mechanisms, aerospace flight control systems, and industrial machinery.
Hypoid gears
Hypoid gears are a type of spiral bevel gear that operate on non-intersecting, offset shafts. The unique geometry of hypoid gears, where the axes of the driving and driven gears do not intersect, allows for larger contact surfaces between the teeth, leading to smoother and quieter operation.
The main advantages of hypoid gears include high torque capacity, reduced noise and vibration, compact design.
Hypoid gears are commonly used in automotive differentials, trucks, and industrial machinery where high torque transmission and quiet operation are essential.
Worm gears
Worm gears consist of a helical gear (the worm) that meshes with a toothed wheel (the worm wheel). The worm resembles a screw, and its unique design allows for a high gear reduction in a compact space, making worm gears useful for applications needing large reductions in speed with high torque.
Key features include high reduction ratio, self-Locking Mechanism, smooth and quiet operation.
Worm gears are widely used in conveyor systems, lifts, hoists, and heavy machinery where compact design, noise reduction, and high torque are beneficial.
Helllical gears
Helical gears are cylindrical gears with angled teeth that spiral around the gear's circumference, forming a helix. This angled design allows for smoother and quieter operation compared to straight-cut gears, as the teeth engage gradually rather than all at once.
The overlapping teeth increase the contact area, allowing helical gears to handle higher loads and transmit more power.
On the other hand, due to the angle of the teeth, helical gears generate an axial force (along the gear shaft), requiring proper bearing support.
Helical gears are commonly found in automotive transmissions, industrial machinery, and other high-speed or high-load applications where smooth power transmission is essential.
Spur gears
Spur gears are the simplest type of gear, featuring straight teeth that are parallel to the gear’s axis. They are commonly used to transmit motion and power between parallel shafts. Easy to manufacture and cost-effective.
The straightforward tooth design allows for efficient power transmission with minimal energy loss.
Unlike hellical gears, spur gears engage abruptly, producing more noise and vibration, which makes them more suitable for low- to moderate-speed applications.
Spur gears are widely used in mechanical systems like clocks, washing machines, and conveyor systems where simplicity, durability, and efficiency are prioritized.
Prototype gear samples
Plastic
Narutaki's Gear Manufacturing Equipment
At Narutaki, we utilize the Matrix GBG-3210 Gear Grinding Machine to deliver exceptional precision and quality in our gear manufacturing processes.
Key Features of the Matrix GBG-3210:
- High Precision Grinding: The GBG-3210 ensures ultra-precise gear grinding, achieving tight tolerances and superior surface finishes for spiral bevel and miter gears.
- Versatile Capabilities: Capable of grinding a wide range of gear sizes and types, this machine provides the flexibility needed to meet diverse industry requirements.
- Advanced Control Systems: Equipped with sophisticated CNC controls, the GBG-3210 offers enhanced automation, consistency, and ease of operation, resulting in high-quality gear production.
- Robust Construction: Built for durability and reliability, the Matrix GBG-3210 can withstand rigorous use, ensuring consistent performance over time.
- Efficient Production: With its high-speed grinding capabilities and efficient workflow, this machine significantly reduces production times while maintaining the highest quality standards.
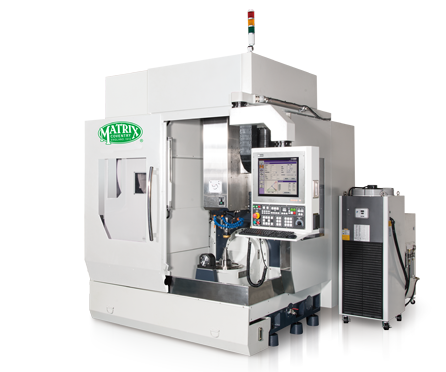
GBG-3210 (CNC Bevel Gear Grinding Machine)
Service Process
STEP 1: Inquiry
Start the process by reaching out to us with your specific gear grinding needs and requirements.
STEP 2: Consultation
Have a thorough consultation to discuss your technical specifications and application details, ensuring we fully understand your needs.
STEP 3: Quotation
Provide a detailed quotation, including cost estimates, timelines, and terms, based on our consultation.
STEP 4: Order Confirmation
Review and approve the quotation, then confirm your order and the agreed terms.
STEP 5: Design and Planning
Review your gear design and offer a comprehensive production plan to ensure precision and efficiency.
STEP 6: Gear Grinding
Perform precision grinding on your gears, achieving the required dimensions and surface finish.
STEP 7: Final Inspection
Conduct thorough testing and inspection to ensure your gears meet all specified requirements and quality standards.
STEP 8: Packaging and Delivery
Securely package your finished gears and coordinate logistics to ensure they are delivered to you safely and on time.
FAQs about gear grinding service
Q.1: What materials can be used for prototype gear production?
Narutaki Industries can prototype gears made from a variety of materials, including high-strength alloy steels, carbon steels, stainless steels, plastic, and specialized materials tailored to meet specific industry requirements.
Q.2: What is the typical lead time for gear prototypes?
The typical lead time for a custom gear prototypes order at Narutaki Industries varies depending on the complexity and quantity of the gears. Generally, it ranges from 3 to 7 weeks from order confirmation to delivery. Expedited services may be available upon request.
Q.3: Do you offer design support or consultation for custom gear designs?
Yes, Narutaki Industries offers services such as designing gears and selecting materials according to the customer's needs. Please contact us even if you need a gear but have not yet decided on the specifications.
Q.4: Do you provide small batch production for gears?
Yes, Narutaki Industries can provide small batch production for gears. Depending on the material and processing method, we can even produce from just one piece.